QUALITY
FROM START TO FINISH
"Quality From Start to Finish" It's not only our philosophy at Winona, it's our tag line! We are an ISO 9001-2015 certified custom coater working to exceed our customer's expectations every day. Whether a powder coating has to withstand harsh environments or resist normal wear and tear, our customers need to know what to expect from our powder coating. Flexibility, color, gloss, adhesion, corrosion resistance, chemical resistance, durability, film thickness, proper curing, and overall appearance are things we test for as part of a quality assurance program.
Winona uses state of the art methodologies to ensure product quality is to the highest standards, specifically:
- Pretreatment monitoring
- Oven Cure Verification
- Thickness testing
- Gloss evaluation
- Color verification
- Cure confirmation
- Adhesion testing
- Mandrel Bend testing
- Visual inspection per customer standard
- Impact Test
- Salt Spray test
- Cyclical Corrosion test
- Weathering test
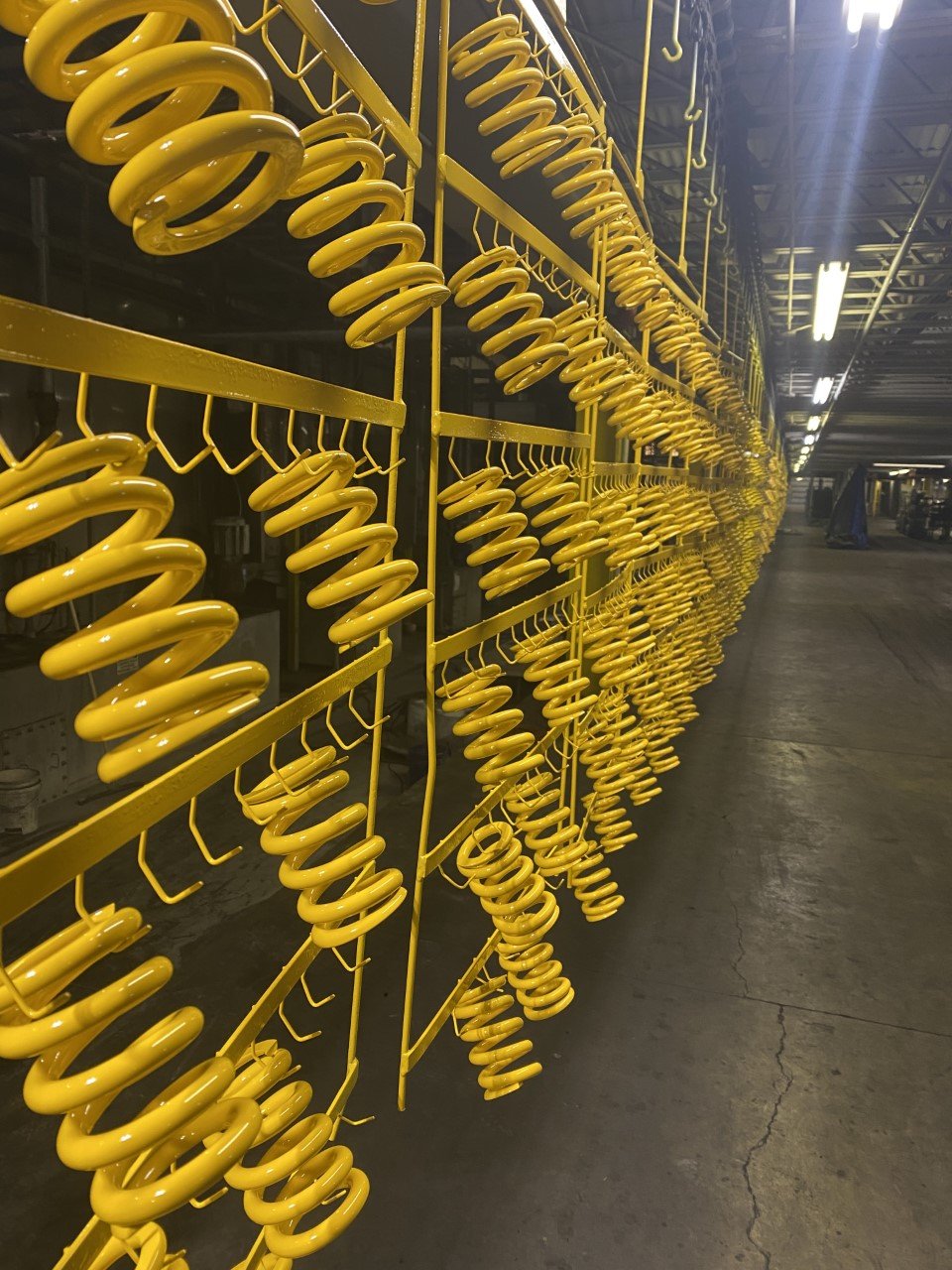
Pretreatment Monitoring
Perhaps one of the most important steps in powder coating is pretreatment. Pretreatment allows for the powder paint's proper adhesion to the substrate and ensures the coating's long term adhesion to provide lasting corrosion resistance. The process requires three steps:
Cleaning:
The first step to proper preparation is to remove soils, oils, oxides, and other contaminants from the part or parts to be coated. Factors to consider include accurate levels to improve soil removal, decrease cleaning time, and provide an optimum surface for the phosphate layer.
Rinse:
Water may be the most important component in the pretreatment process. 95% or more of the pretreatment process involves water.
Poor water quality results in:
- Adhesion failure
- Rust
- Warranty claims
- High water treatment costs
- Environmental compliance issues
Good water quality is an essential key to your pretreatment process. At Winona Powder Coating, our water quality is monitored and controlled routinely, efficiently, and effectively to ensure the best coating.
Chemical Conversion of the Surface:
Common Types Include:
- Iron Phosphate for Ferrous Metals
- Chromate Conversion for Aluminum
Conversion coatings are a complete film that changes the physical and chemical nature of the metal surface. A clean surface is required for the reaction.
The neutralizer stabilizes the conversion coating, while the temperature of the rinse increases the solubility of the residues and improves dry off time. Proper flow patterns and rinse volume promote a more thorough rinse. Overflows and screens are used for the removal of the soils, oils, and other contaminants.
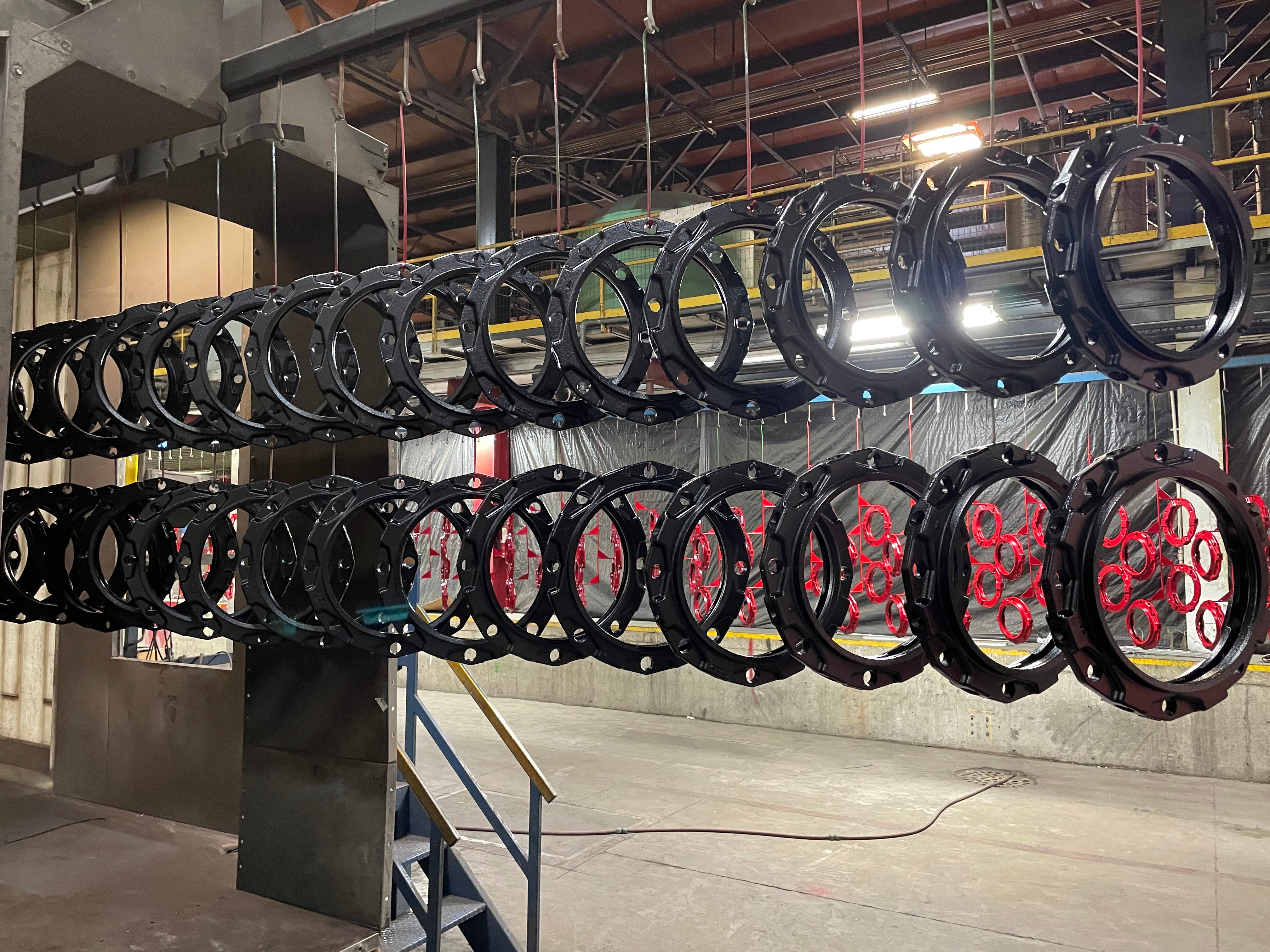
Oven Cure Verification
Cure ovens are an integral part of any powder coating system. Problems with them can mean the difference between having fully cured parts or having field failures, such as coating adhesion difficulties. With little effort, a curing oven can consistently provide the energy required to cure the applied powder paint.
On the one hand, convection ovens are the most complex cure system, requiring the most upkeep. Burners, blowers, ductwork, and associated moving parts need periodic preventive maintenance. On the other hand, infrared systems are relatively simple to maintain because they do not have moving parts (except for exhaust fans). As long as the emitters are in good operating condition and properly maintained, they can continue to cure your coated parts.
Preventive Maintenance
Periodic inspection and maintenance can go a long way in reducing costly downtime or rejected parts. The most important things to check are the oven’s air balance, cleanliness, bearing lubricant, components, and safety devices. Following our weekly, monthly, and annual maintenance schedules has proven to keep our cure ovens tuned effectively.
Oven dirt is a typical problem in many powder coating systems. Our monthly clean-up will ensure the highest coating quality on your parts.
Annual maintenance and inspection schedule. Many plants shut down annually to do system checks that are too time-consuming to do during the production year. These inspections include:
- Ignition
- Burner
- Flame failure system
- Combustion controls
- Pipes and wires
- Thermocouples
- Automatic fire suppression
- Operating sequences
If a component is suspect, we replace it right away instead of waiting until it fails during production. At Winona Powder Coating, maintenance is not taken lightly or ignored to ensure trouble-free throughout our production.
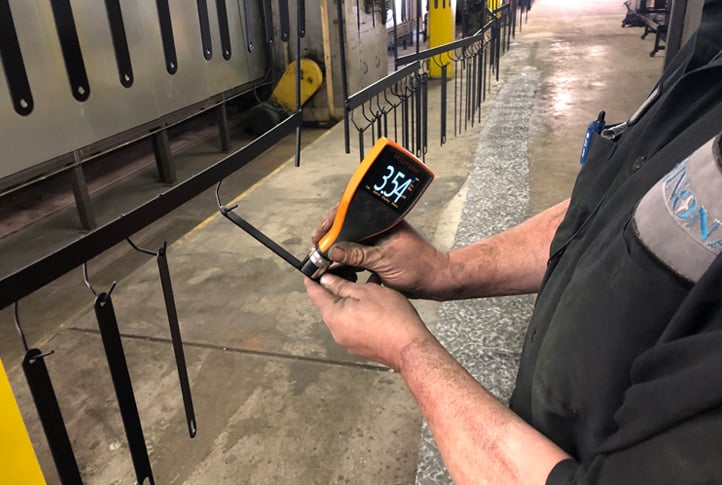
Thickness Testing
A thickness test determines the thickness of the powder on the part once it's been cured. This is generally confirmed with a Dry Film Thickness gauge. A common range we look for is 2-4 dry mils (thousandths of an inch). A coating of 2-4 mils usually provides complete coverage of powder paint. Ensuring that equipment coatings have a certain thickness is essential in maintaining their effectiveness.
Whether initially checking before curing or re-examining the thickness after the coating has been in use for some time, a good thickness reading ensures extended life for coated parts.
Both types of coating thickness are measured in mils, indicating one-thousandth of an inch. Wet paint tends to produce thinner coatings per application than powder coatings due to solvents' evaporation in the former's drying process.
Powder coating thickness can be measured in many ways, but they all fall under two categories:
- Testing Before Curing
- Testing After Curing
Testing before curing measures the powder's thickness before it crosslinks into the resulting, even coating. Two of the methods involve a comb and a probe, measure the powder's height – the thickness is determined by factoring the reduction factor against the height measurement. Both methods displace powder to take a measurement, leading to an imperfection in the coating after curing. These methods help establish that the coating is sufficiently thick during production but do nothing to help after the equipment has been cured.
The third method uses an ultrasonic reader, non-destructive, to predict the cured coating's thickness. Testing after curing is more commonly used in quality control inspections. Performed after the equipment is already in use, this can be achieved in multiple ways:
Mechanical Magnetic Gauges: a magnet is stuck on the test material and then pulled off – the amount of pressure needed to separate gauge from coating determines the thickness.
Ultrasonic Gauge: a probe on the test material sends an ultrasonic pulse that travels through the coating, hits the substrate, and bounces back. Converts the time-lapse to a thickness reading.
Micrometer: measure the substrate's thickness with coating vs. substrate without coating – the difference is the coating thickness.
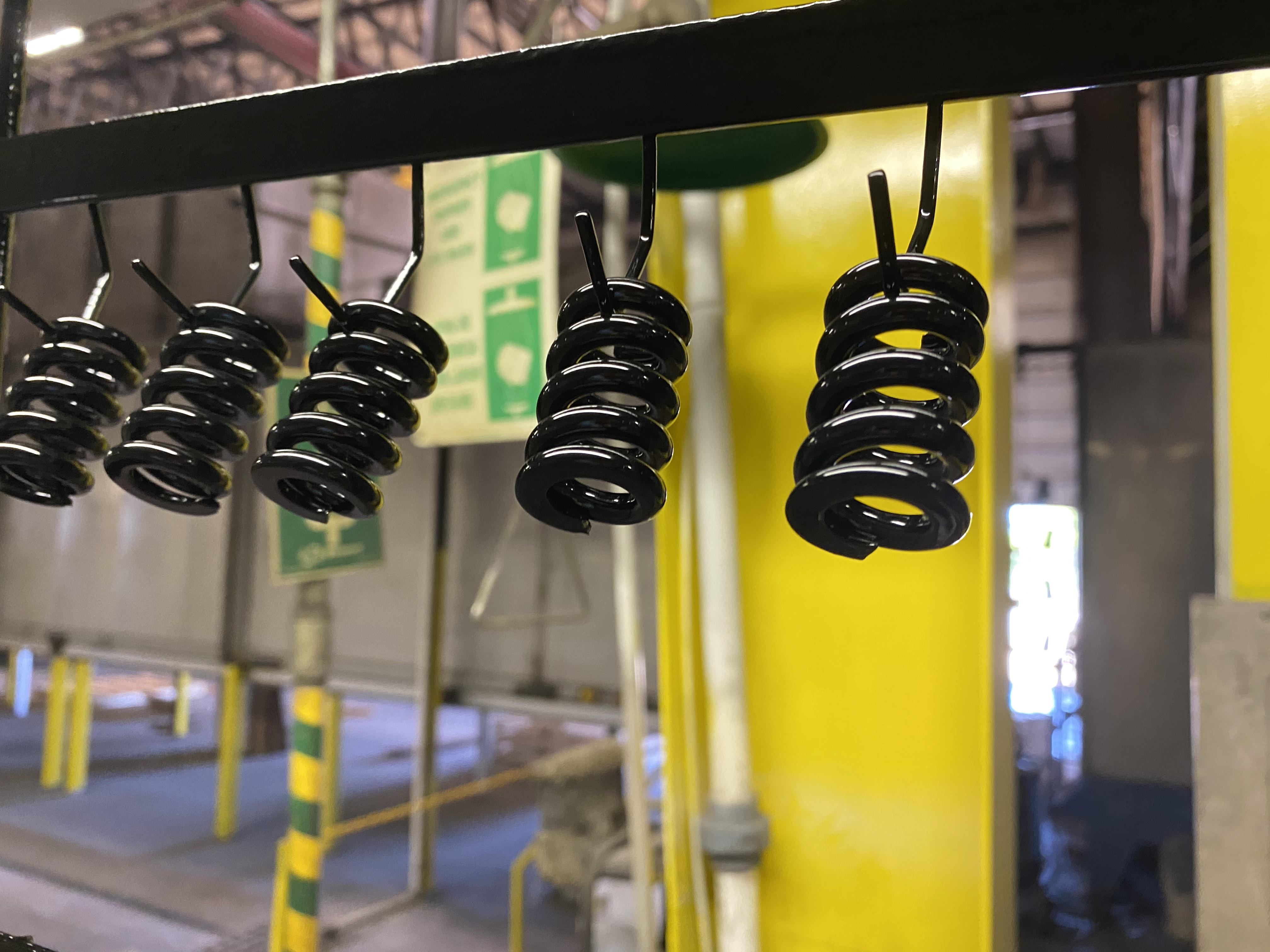
Gloss Evaluation
One of the benefits of powder coating is how great the finished product looks. All your products are inspected before shipment to ensure there are no gaps in coverage, bubbles, warping, or poor coating application. If your quality assurance manager is actively looking for defects, problems with the powder coating, or the product can be fixed before delivery.
Many factors can cause appearance issues. Contamination is usually the biggest problem. Shop dirt, welding debris, sanding dust, or other airborne contaminants can get on the parts. These substances can cause the powder to react negatively or fail to cover the contamination. Proper cleaning and pretreatment can address these issues.
Unfortunately, improper cleaning contributes to many appearance issues. Ignoring rust or residue can prove costly in the long run. The use of poorly mixed or overly-diluted chemicals, the application of inappropriate detergents, and other pretreatment shortcomings related to carelessness can also cause notable finish problems.
Sometimes water in compressed air lines or high humidity in the shop environment can cause the powder to clump and generate unwanted appearance issues. Evaluating your process by eliminating one variable at a time is crucial for discovering what’s causing the issue.
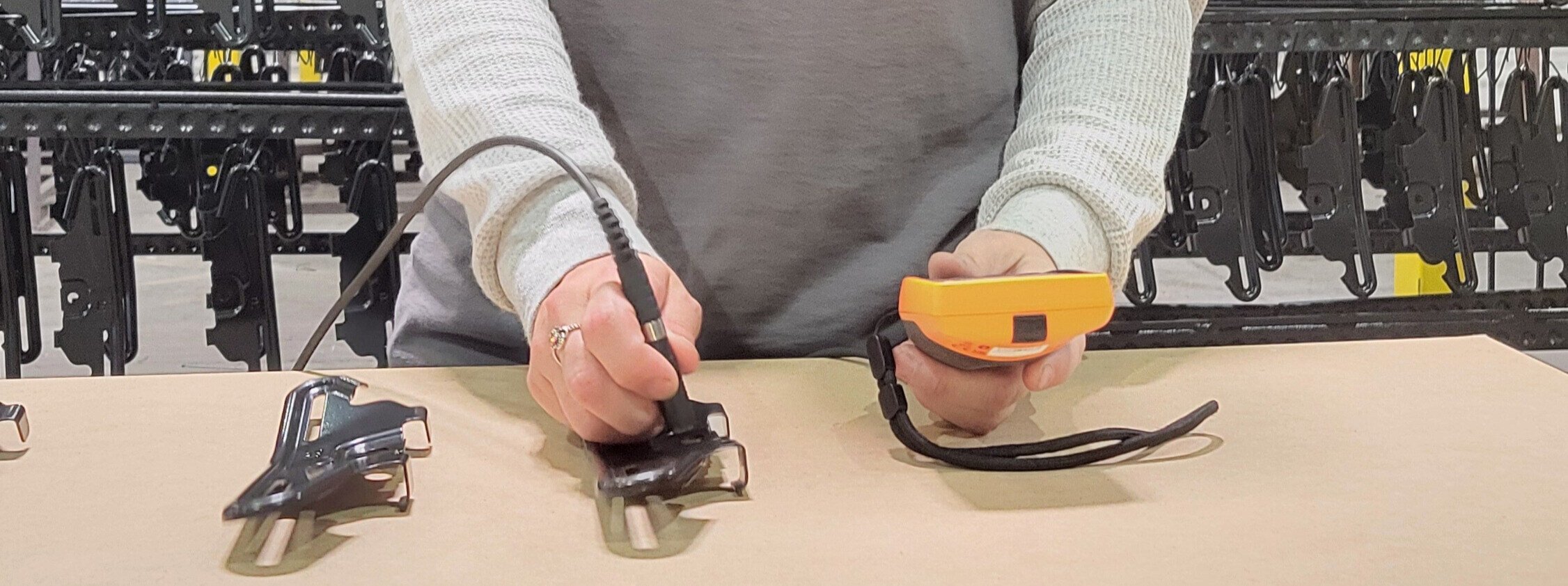
Cure Confirmation
When we talk about “cure” in quality control, we’re discussing the correct temperature and dwell time that allows the powder coat to achieve it’s formulated hardness and chemical resistance properties. When testing the cure, we make sure that there aren’t any overbake areas, where the powder has cured in a dry and brittle fashion, or underbake, where the powder has not completely cured.
Proper curing is verified by rubbing a methyl ethyl ketone-soaked cotton swab lightly over a cured panel or part. If the finish deteriorates to the point that you expose bare metal, the cure is lacking, or the powder is defective.
If your parts fail their cure tests, the temperature in the oven or dwell time in the oven may need to be increased. If this is the case, we will carefully adjust the process not to overcure. That can cause issues such as adhesion failure, dulling of gloss, or yellowing and browning of the color, especially if coating white.
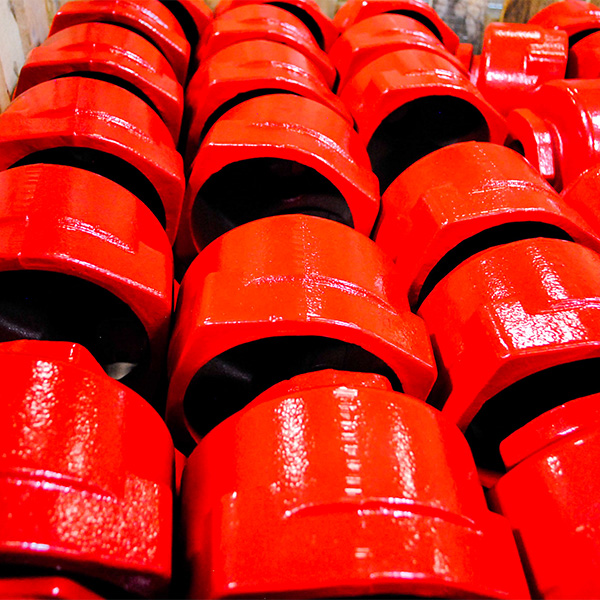
Adhesion Testing
Adhesion testing measures how well the powder paint sticks to the part once it is fully cured. As with the cure test, the adhesion test results can be altered by either over- or underbaking.
We perform the adhesion test on a test panel that has already been coated and cured. Using a utility knife, we scribe a section of the part’s coating with a grid-like appearance. Making sure to cut through the coating to the metal.
After making the cuts, we put a piece of tape over the grid and smooth out any air bubbles and remove the tape quickly. An acceptable result will show only a little of the powder coming off from the grid cuts. If a square or two of coating is removed, adhesion can be suspect. If the coating comes off in a sheet, then it is an adhesion failure.
Several factors can cause adhesion failures. One of the first places to look is metal preparation. If the metal is too slick or oily, powder paint will not be able to stick to the surface. This is why we are careful to make sure the prepped part is clean and etched/abraded. Overcure can also cause the powder to become so brittle that it will easily pull away from the metal. Old powder may have issues that can cause a lack of adhesion as well.
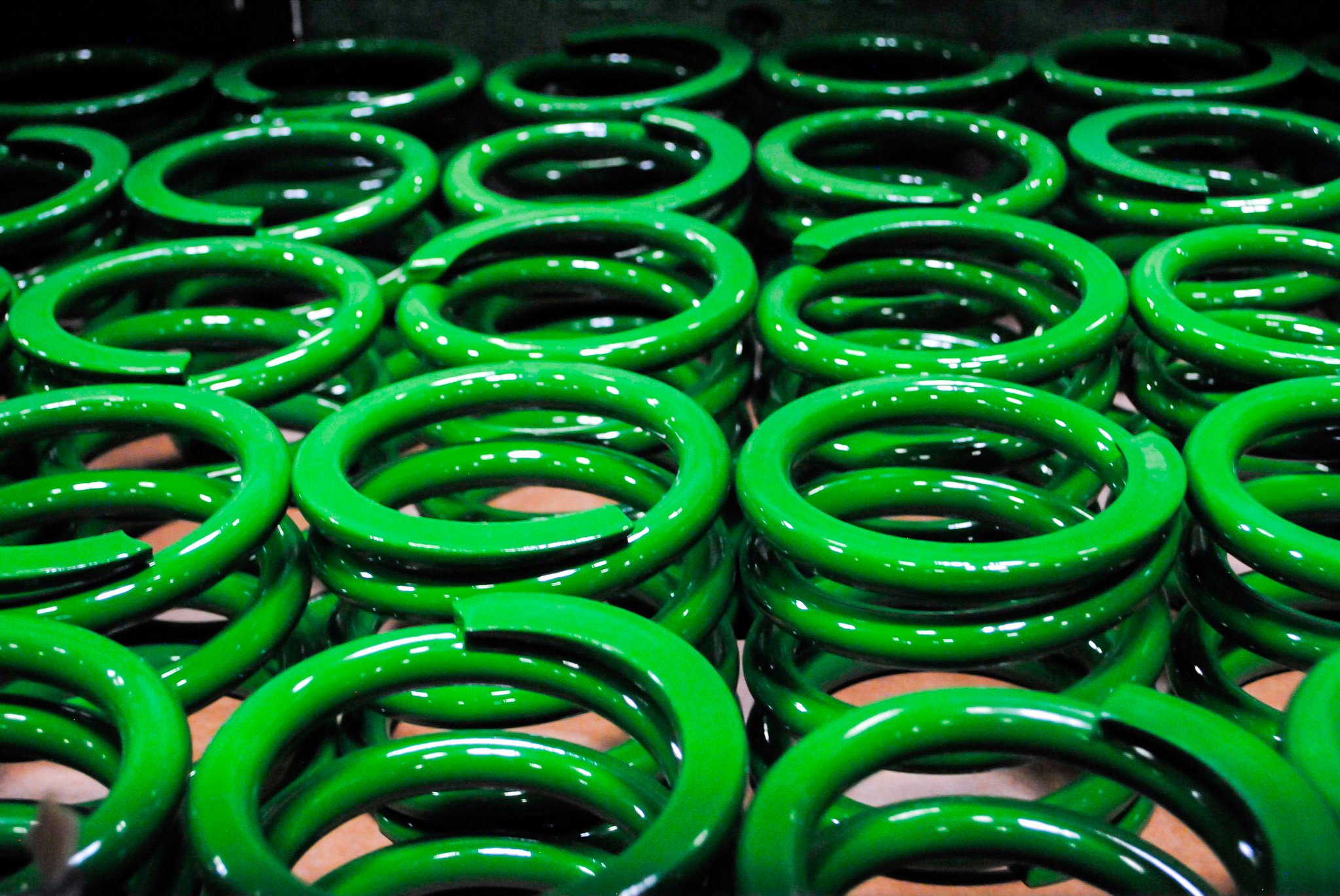
Visual Inspection Per Customer Standard
The second part of your appearance testing routine involves our team taking time to communicate with our customers. Every customer should have an idea of what they consider to be an acceptable finish, but it may take some discussion to determine what’s realistic and measurable. A finish standard can be as simple as no more than two visible surface imperfections per square foot. Gloss and color standards may also be included. If a customer has exact requirements, we make certain the customer receives exactly what they expect.
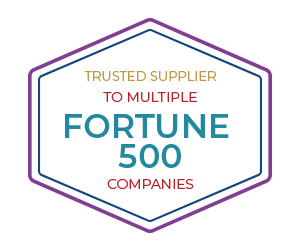
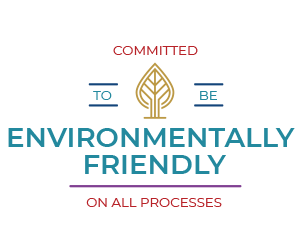
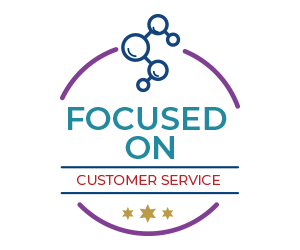
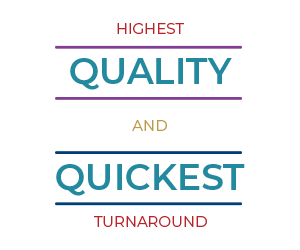